Active Soil Depressurization has proven to be a very reliable means by which radon laden soil gas can be reduced from indoor environments. In its simplicity, one can even say it is elegant. Core a hole, dig out a pit, connect a fan and pipe, and voila, problem solved. However, there are situations where we may want to think “outside the pit” when dealing with larger buildings, such as schools and offices where heating ventilation and air conditioning (HVAC) systems play a large role.
It is rare that all rooms within a school are elevated. Plotting radon readings on a floor plan helps identify areas of concern. When one is asked to explain why one portion of a building is elevated and others are not, the stock answer I typically get is “because there must be a high radium content in the sub-grade under those rooms.” NOT! The likelihood of large differences in subgrade make-up beneath the footprint of a building is low. Granted there can be some deep fissures that provide a unique pathway to a specific location, but that is rare and the imported fill provided under large buildings dampens this effect.
What is more likely when seeing localized areas of high radon is the effect that an imbalanced or even disabled HVAC system can have. Imbalanced HVAC systems can create tremendous negative pressures in localized areas causing radon to preferentially enter those rooms. Even to the point where an ASD system cannot overcome them. Hence, less than effective results.
The advice I provide students is to go back to the building and work with building maintenance personnel to understand the HVAC system. The key question you are trying to answer is: Why are these rooms low and the other ones high? Find out what is different about the low rooms and, if you are able to make the high rooms operate like the low rooms, the problem is either solved or the ASD system can function as desired. Here are a few tips:
Fresh Air Make-up
Most buildings constructed in the last 50 plus years had provisions within their HVAC systems for the introduction of outdoor air when the building is occupied. This involves ductwork to the air handler, typically with a damper that is controlled by a motor that is controlled by an energy management system that closes the damper during off hours to reduce energy costs. This outdoor air may be provided to large central air handlers or be provided to unit ventilators serving individual rooms.
First verify outdoor air provisions exist. Then verify they are working and actually allowing fresh air in. I have seen cases where plywood has been placed over these to reduce energy costs. I have also seen where the damper motor is operating and the energy management system is telling the damper to open, but the linkage to the damper is either broken or has been disconnected.
There are often protective devices that will close an outdoor damper if the outdoor air gets too cold to where a coil may freeze (called Freeze Stats). These are set up such that if the sensor or control fails, the damper will return to a closed position, i.e. “fail safe.” Many times these controls have failed without maintenance being aware of it or lack of maintenance funds to repair. Failure of a damper control in one room’s unit ventilator but not in another room can easily account for significantly different radon measurements in these rooms.
There are also filters on the fresh air make-up and sometimes dehumidification coils. These filters need to be changed regularly and the coils cleaned. If not, the required air flow is reduced. If you are told they are working perfectly, take your smoke bottle and prove it to yourself. Many times the HVAC systems serving the elevated rooms are not allowing air in. In one case, I asked the maintenance person when was the last time the filters were changed. The answer was “Never” because the access to the filter (from the outside) had been compromised when they had repointed the exterior brick 20 years ago. After a little hammer and chisel work, the situation was fixed and new filters installed with two results: The radon went down and the occupants of the room noticed a significant improvement in air quality. All without a Pit.
Another example was an airport where one terminal was elevated and the other was not. Due to the size of the airport, dozens of ASD systems would have been required to fully treat the subject terminal. When talking with maintenance personnel they bemoaned how the HVAC system had been installed on the “bad” wing such that they could not clean the dehumidification coils like they could on the “good” wing. Again some modifications were made, coil cleaned and same result: Low radon, better air quality.
When determining a strategy, walk into the subject rooms and in addition to looking down searching for footings also look up at the ceiling vents. Are there both a supply and a return? Sometimes a partition wall has been added turning one room into two rooms and the HVAC ductwork is not modified. This can result in one room having the supply air and the other having the return air. Needless to say, the one with just a return is under negative pressure and is the high radon room. Adding the ductwork to both sides so there is balance can be an easy task for the school maintenance staff.
Although there are other things to look at, I will provide one more suggestion after you are convinced that the HVAC is working properly or perhaps even as a first step. Radon levels within a building equipped with an energy management system, as is common in buildings that are not occupied 24-7, will vary more with HVAC operation than diurnal variations as we see in residences. It is likely the testing methodology that identified the radon problem was a short-term integrating device. These are great indicators of potential but as a follow-up, utilize a continuous monitor to allow you to differentiate radon levels between occupied and unoccupied periods. In other words, the buildings HVAC system may already be reducing radon exposures while people are within it. I have seen radon levels above 20 at night but less than 1 during the day. That is the power of a properly operating HVAC system.
So, in closing, Active Soil Depressurization is a great technique but as radon professionals we can also be building scientists and analyze the situation and get to the root of the problem with lower costs to your client and greater immediate benefit to their employees and students. In other words: Think Outside the Pit!
Thinking Outside the Pit
Douglas L. Kladder, Director CERTI
Active Soil Depressurization has proven to be a very reliable means by which radon laden soil gas can be reduced from indoor environments. In its simplicity, one can even say it is elegant. Core a hole, dig out a pit, connect a fan and pipe, and voila, problem solved. However, there are situations where we may want to think “outside the pit” when dealing with larger buildings, such as schools and offices where heating ventilation and air conditioning (HVAC) systems play a large role.
It is rare that all rooms within a school are elevated. Plotting radon readings on a floor plan helps identify areas of concern. When one is asked to explain why one portion of a building is elevated and others are not, the stock answer I typically get is “because there must be a high radium content in the sub-grade under those rooms.” NOT! The likelihood of large differences in subgrade make-up beneath the footprint of a building is low. Granted there can be some deep fissures that provide a unique pathway to a specific location, but that is rare and the imported fill provided under large buildings dampens this effect.
What is more likely when seeing localized areas of high radon is the effect that an imbalanced or even disabled HVAC system can have. Imbalanced HVAC systems can create tremendous negative pressures in localized areas causing radon to preferentially enter those rooms. Even to the point where an ASD system cannot overcome them. Hence, less than effective results.
The advice I provide students is to go back to the building and work with building maintenance personnel to understand the HVAC system. The key question you are trying to answer is: Why are these rooms low and the other ones high? Find out what is different about the low rooms and, if you are able to make the high rooms operate like the low rooms, the problem is either solved or the ASD system can function as desired. Here are a few tips:
Fresh Air Make-up
Most buildings constructed in the last 50 plus years had provisions within their HVAC systems for the introduction of outdoor air when the building is occupied. This involves ductwork to the air handler, typically with a damper that is controlled by a motor that is controlled by an energy management system that closes the damper during off hours to reduce energy costs. This outdoor air may be provided to large central air handlers or be provided to unit ventilators serving individual rooms.
There are often protective devices that will close an outdoor damper if the outdoor air gets too cold to where a coil may freeze (called Freeze Stats). These are set up such that if the sensor or control fails, the damper will return to a closed position, i.e. “fail safe.” Many times these controls have failed without maintenance being aware of it or lack of maintenance funds to repair. Failure of a damper control in one room’s unit ventilator but not in another room can easily account for significantly different radon measurements in these rooms.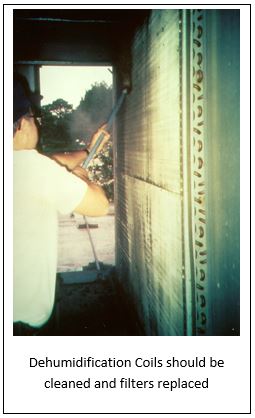
There are also filters on the fresh air make-up and sometimes dehumidification coils. These filters need to be changed regularly and the coils cleaned. If not, the required air flow is reduced. If you are told they are working perfectly, take your smoke bottle and prove it to yourself. Many times the HVAC systems serving the elevated rooms are not allowing air in. In one case, I asked the maintenance person when was the last time the filters were changed. The answer was “Never” because the access to the filter (from the outside) had been compromised when they had repointed the exterior brick 20 years ago. After a little hammer and chisel work, the situation was fixed and new filters installed with two results: The radon went down and the occupants of the room noticed a significant improvement in air quality. All without a Pit.
Another example was an airport where one terminal was elevated and the other was not. Due to the size of the airport, dozens of ASD systems would have been required to fully treat the subject terminal. When talking with maintenance personnel they bemoaned how the HVAC system had been installed on the “bad” wing such that they could not clean the dehumidification coils like they could on the “good” wing. Again some modifications were made, coil cleaned and same result: Low radon, better air quality.
When determining a strategy, walk into the subject rooms and in addition to looking down searching for footings also look up at the ceiling vents. Are there both a supply and a return? Sometimes a partition wall has been added turning one room into two rooms and the HVAC ductwork is not modified. This can result in one room having the supply air and the other having the return air. Needless to say, the one with just a return is under negative pressure and is the high radon room. Adding the ductwork to both sides so there is balance can be an easy task for the school maintenance staff.
So, in closing, Active Soil Depressurization is a great technique but as radon professionals we can also be building scientists and analyze the situation and get to the root of the problem with lower costs to your client and greater immediate benefit to their employees and students. In other words: Think Outside the Pit!
If you would like more information or this topic interests you, we recommend the CE Course – C-16-108 – Addressing Radon in Daycare Facilities, Schools and Large Buildings
Douglas L. Kladder,
Director, CERTI
Archives
Recent Posts
Radon Health Effects: Are We Moving Away From Science?
April 20, 2023What Good is a DIY Book for Radon Professionals??
April 20, 2023Explaining the Purpose of Closed Building Conditions When Measuring Radon
May 5, 2022Font Resizer
A Decrease font size. A Reset font size. A Increase font size.